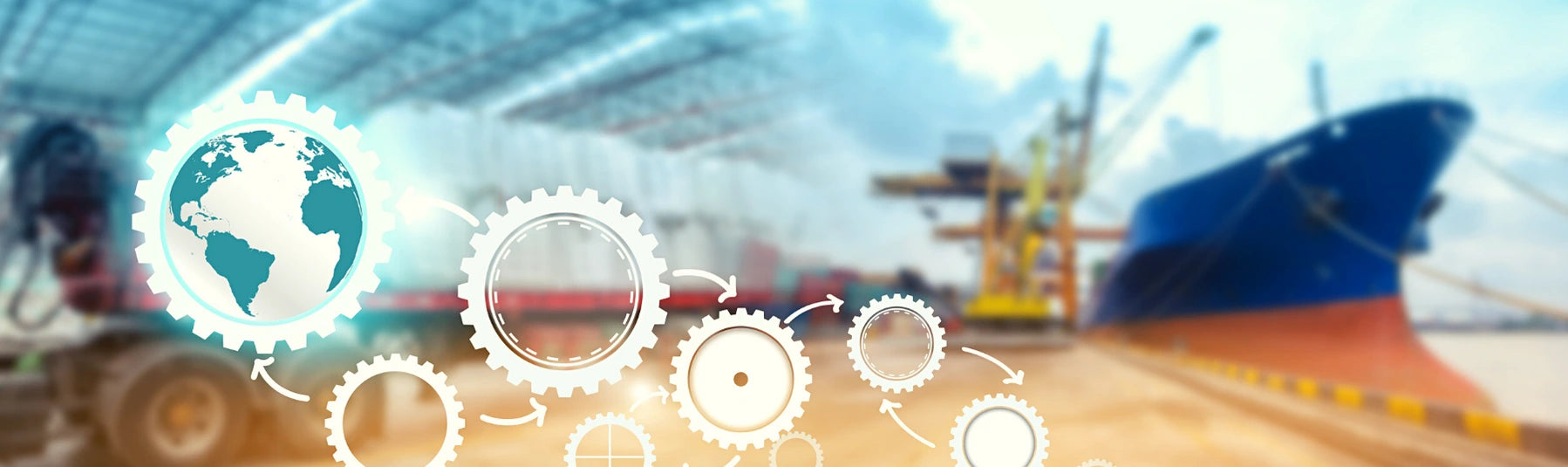
How the Pandemic Global Supply Chain Impacts Your Domestic Coffee Roastery — And What You Can Do About It
If you own a coffee roasting business, then I’m betting you’re painfully aware of how the pandemic’s impact on the global supply chain has affected not only worldwide commerce but also your coffee roasting business.
I was scrolling through LinkedIn recently and saw a post by supply chain executive Daniel “Mr. Supply Chain” Stanton. He was sharing his thoughts on how the pandemic has uncovered the dire need to make our global supply ecosystem more resilient. His comments stemmed from a recent CNN article exploring how supply chain disruptions have impacted the flow of shipping containers — and how their increasing costs are having a crippling effect on global commerce.
I thought Stanton’s comments and the CNN article were spot on. At CoffeeTec, we move products from all over the world and thankfully, we have a logistics expert of 40 years using that experience to help us get coffee roasters to our customers as efficiently as possible. I’ve pretty much seen it all when it comes to dealing with issues and delays tied to transporting green coffee beans and industrial and commercial coffee roasting equipment. In fact, I wrote about some of the issues we see, and how we can best prepare for them, in October 2020 — just about eight months into the pandemic.
Now, 18 months into the pandemic, we’re witnessing just how much COVID-19 has brought a whole new level of complication to how the global supply chain moves and operates, even in the coffee industry. Just last month, an analyst at Seattle-based Atlas Coffee Importers penned this humorous fictionalized example of how the global logistics crisis impacts coffee imports.
Our logistics team simply hasn’t dealt with any of the usual supply chain challenges — transportation, shipping costs, materials availability, manpower, and more — at this magnitude before. Given this, I thought it might be helpful to expand on my prior article, share what we’re seeing now, and translate this into a few tips to help you best prepare for a situation that likely won’t go away any time soon.
The Big 4 Disruptors
There are many links in the supply chain that, when broken, disrupt the entire supply-demand process — including for coffee roasting equipment. Here are what I consider to be the top 4 disruptors:
- Shortage of Parts
Parts everywhere, especially computer and semiconductor chips, are coming up short. Just last month, Toyota announced it would reduce its global auto production by 40 percent, due to a lack of parts. Fully automated roasting machines normally 30-kilo and above use some sort of chip, so we’re seeing that greatly impact production time and speed-to-market. A new coffee roaster build can take up to eight months. With this parts shortage, it might easily take double the amount of time to get that roaster.
- Price Increases for Raw Materials
The price of all raw materials is in constant fluctuation based on the market. The pandemic has caused increased materials shortage due to factory closures, logistical issues, and lack of labor force due to quarantines. This, in turn, drives up the price of these much-needed materials and components. Just look at high-carbon steel. Demand has been on the rise since Summer 2022, with reports of a total cost increase of over 200%. High polished stainless steel has reportedly increased 300%. How does this impact you? Well, your roaster, silos, and other roasting equipment are made from or have parts made from both of these materials — yielding production delays and price increases.
- Spike in Global Shipping Prices
The pandemic’s impact on shipping costs has been far-reaching — from domestic freight lines to ocean cargo containers. Although cargo containers travel globally, approximately 95% of them are made in China. Due to container hoarding (and other factors), prices have increased from roughly $4,000 to $14,000 a container. The New York Times reported on how these massive price spikes are impacting different consumer industries.
For CoffeeTec's business, our logistics expert Frank Ciofalo tells us that shipping rates have tripled since January 2020 for both air and sea cargo.
- Labor and Machinery Shortage at Ports
The pandemic’s ripple effect on the global supply chain is also seen in severe labor shortages due to quarantining, plants closing operations, or people quitting their jobs. It has also impacted the availability of specialty trucks and racks/chassis needed to accept incoming product shipments at the ports.
Ciofalo explains: “Ports are overburdened with lack of chassis to load containers on. These new container ships hold 15,000 to 18,000 containers and there is no space in the ports when two or three vessels arrive at the same time. Vessels are having to drop anchor in the harbor waiting for a berth for the vessel to dock to allow containers to be discharged.”
Land transport is also feeling the repercussions of this global backlog. Ciofalo adds: “Trucking companies are swamped with excess containers to deliver, but they lack drivers. Many truckers are booked up to more than a month in advance to pick up a client’s container. The ports are not granting these importers storage privileges if their trucking company can’t get the container picked up by the port’s “last free day.” The result? Importers are paying over $400 per day.
What Does This Mean For Coffee Roasteries?
I suggest the below four tips to help you better manage your logistics and equipment needs —and keep your coffee roasting business running smoothly:
- Adjust your time expectations. Everything will just take longer to reach your roastery, including your packaging supplies. Plan as far in advance as possible.
- Save money! You’ll need to save more than usual and watch your pricing to keep up with price increases and inflation.
- Take an inventory. Take stock of your roastery’s items that can go bad or be in short supply: thermo-couplers, bearings, backup motors, packaging, and of course, green coffee supply. Now is the time to track down what you can. CoffeeTec has good sources for some of this smaller equipment.
- Maintain your equipment. Lastly, put extra effort into maintaining your equipment. Keep everything clean and in good operating condition because it might have to be put to use for longer than you expect.
How CoffeeTec Can Help
We take a consultative approach to matching our buyers to used and new equipment, meaning that we take time to understand what you’re looking for to keep your roastery running. We can also advise on your roastery plans and logistics in light of pandemic supply chain disruptions. Or, perhaps you’re looking to sell and move into some different equipment.
Even with the present surge of such supply-demand challenges, we aim to maintain our usual high service levels in supplying you with your coffee roasting equipment. We can do this in big part because of our relationships with our private sellers, buyers, and vendors we represent. And, if we spot any roadblocks, we’ll help troubleshoot and identify alternative roasting equipment options. I hope this brief overview and suggested tips have been helpful and I look forward to the continued success of your coffee business.
Leave a comment